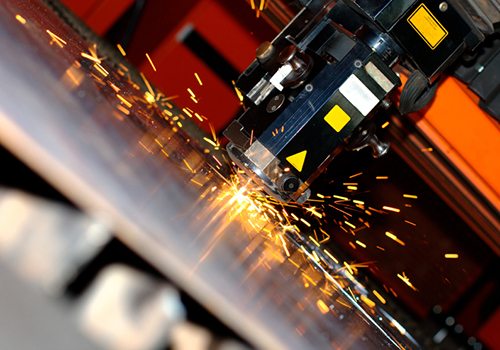
The Next Generation Manufacturing Study illustrates strategies that will carry manufacturing firms into the future.
While the U.S. manufacturing industry is competitive and widely recognized as a critical component in America’s continued economic recovery and job creation efforts, a national study reveals that we are at a critical point in time for American small manufacturers to address certain challenges so they can continue to compete in the global market.
The bi-annual Next Generation Manufacturing (NGM) Study, last released in October 2013, measures manufacturers’ readiness, support systems and resources, and performance in six key strategic areas necessary for world-class manufacturing and future success. The data shows manufacturing organizations that achieve world-class status in at least two of the NGM strategies and maintain industry-average levels in the other four areas are in the best position for long-term survival.
However, the data also finds that most of these manufacturers—successful as they may be today—aren’t investing in the strategies that will carry their firms into tomorrow. Many of these trends still hold true today.
An Execution Gap
“The study data identifies an enormous execution gap—the difference between the number of firms that recognize the importance of a particular NGM strategy, and the number that comes close to or that achieved world-class status in that strategy,” says John Brandt, founder and CEO of the Manufacturing Performance Institute (MPI). For example, the study found:
- Ninety percent of manufacturers believe superior process improvement is important, whereas only 44 percent of those manufacturers are near or currently at world-class status in process improvements.
- While human capital management is an issue, NGM data suggests few manufacturers are taking initiative to address talent shortages. Sixty-nine percent of manufacturing executives have the leadership and talent to drive world-class, customer-focused innovation, but only 37 percent have talent development programs to support world-class, customer-focused innovation.
- Most manufacturers have the tools, technologies and business equipment they need today, but those tools won’t meet the needs of the future. Only 11 percent of manufacturers describe their tools and business equipment as “state-of-the-art” and capable of providing long-term support for world-class supply-chain management.
- Thirty-three percent of manufacturing executives anticipate a planned leadership succession in the next five years, and another 28 percent of executives indicate a succession may occur.
“Given the global competitive landscape and constant change through technology, it is no surprise the Next Generation Manufacturing Study highlights that small and medium-sized manufacturers must continue to transform in order to remain competitive,” according to David Boulay, IMEC president. “The real challenge before us—manufacturing and economic development leaders alike—is to focus on closing this execution gap so we can remain competitive.”
How Manufacturers Are Approaching Improvement
- Continuous improvement. While highly productive, cost pressures faced by manufacturers are tremendous. Integrating approaches in lean, six sigma and new technologies such as robotics and 3D printing will support the improvement process and encourage sustained implementation.
- Innovation and top-line growth. Market differentiation in a crowded field can be difficult, but new services or product features offer manufacturers an opportunity to demonstrate faster, leaner, high-quality production to stay ahead of the curve.
- Supply chain. Exports, reshoring and total cost of ownership are popular terms in the field of supply chain optimization. How to best serve the markets with the least potential risks is the key to promoting a better flow of product from supplier to customer.
- Sustainability. Greater consumer demand has emerged on the focus of and relationship with impacts on the environment. Companies are building business models based on the full life cycle of products. Entering renewable markets and making sustainable improvements inside facilities will have strong but incremental impacts for the long run.
- Workforce. Productivity means more output with less input; this is changing the jobs requiring higher skills. Various studies and industry trends indicate that a large majority of companies find less than half of their workforce have the necessary technical skills, problem solving skills and work ethic to remain competitive. By focusing on the people side of the business and creating an environment of skill acquisition—from hiring and onboarding through training and strengthening of key abilities—a manufacturer’s workforce will succeed.
In order to increase the opportunities available and focus on key improvement areas to close the execution gap, MPI, in coordination with the American Small Manufacturers Coalition (ASMC) and Manufacturing Extension Partnership (NIST-MEP), introduced the Next Generation Manufacturing (NGM) Assessment Tool in the spring of 2014 to help identify and measure strategic benchmarks in the six key areas of manufacturing businesses.
The NGM Assessment Tool offers a quick and free mechanism for manufacturers to search and benchmark their progress toward world-class status by comparing their responses to thousands of former study participants. Based on six NGM strategies, it provides manufacturers a foundation for strategic planning by identifying opportunities and insight for improvement. The assessment tool is completely free to all manufacturers and based on the NGM Study results of U.S. manufacturers nationwide. To get started, visit NextGenMfgTool.com.
Help Beyond Your Own Walls
Manufacturers routinely seek external support from outside organizations in dealing with a range of activities. Not surprisingly, larger manufacturers (based on revenues) with deeper pockets are better able to look for external support than smaller organizations. But a majority of manufacturers that have used outside resources report positive impacts from industry associations, state manufacturing associations (including IMEC and other state MEP centers) and consulting firms.
Manufacturers looking to implement NGM strategies don’t need to go it alone. A wide array of organizations—public, nonprofit and private—are already helping thousands of manufacturers implement the strategies and sustaining results. To learn more about Next Generation Manufacturing or to get started on your improvement journey, visit imec.org.
The Manufacturing Performance Institute conducted this research based on recent survey responses of manufacturing executives nationwide. The next study will be conducted in late summer 2015. For more information, visit smallmanufacturers.org/news. iBi