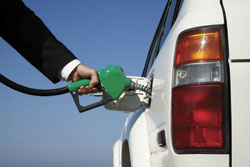
Subsequent to President Bush’s 2005 State of the Union Address and the Energy Policy Act of 2005—which set an aggressive renewable fuel standard—ethanol plants were built left and right.
Conservative rural investors, private equity firms and even Wall Street have taken notice. According to the Renewable Fuels Association, six billion gallons of ethanol are produced on an annual basis, and another six billion gallons of production are under construction.
Introduction to Ethanol and Biodiesel
Ethanol is a commercial manufacturing process that breaks down natural starches through a fermentation process into 95 percent pure alcohol—a process similar to old fashioned moonshine. The predominant form of commercial production is based on the utilization of standard No. 2 yellow corn, which has significant concentrations of starch in the endosperm (near the center of the kernel). The traditional process grinds the corn kernel and adds chemical catalysts and heat to begin the fermentation process. The dominant byproduct of the traditional corn-based ethanol process is called distillers grain, which can be sold wet or dry. Approximately 2.8 gallons of ethanol can be derived from a bushel (60 pounds) of corn.
Biodiesel is an emerging business segment of the renewable fuels sector. Biodiesel production involves a chemical process that derives fuel-grade diesel and industrial glycerin from oil feed stocks such as food, soybean and other waste oils. Many of the analyticals are similar to the early-stage ethanol boom, and production efficiencies, development of the fuel infrastructure and by-product value streams will likely advance this segment in the coming years.
New Technologies and Sectors
The Renewable Fuels Association projects that 140 billion gallons of gasoline are consumed yearly in the United States. The projected 12 billion gallons of ethanol production in the “pipeline” represents almost 10 percent of the gasoline consumed in the U.S. If proposed legislation becomes law, the renewable fuel standard will be set at nearly 35 billion gallons, or approximately 25 percent of the gasoline consumed in the U.S. The incredible expansion of fuel production has an industrial impact in a number of categories, but primarily in integrated business enterprises and non-integrated businesses in the form of supply chain cost variances.
Traditional product manufacturers are benefiting from the development of new technologies to advance production efficiencies, such as cellulosic production, fractionation and oil extraction. While many of these technologies have yet to reach widespread commercial usage, they will certainly expand existing product lines of machinery and equipment.
Cellulosic ethanol is produced in a manner similar to traditional corn-based ethanol production. The difference primarily relates to the feedstock or raw material—natural sugars in plant cells. Since many products have significant natural material contents, cellulosic ethanol can be derived in some context from almost any natural compound. This new technology is focused on organic materials—such as trees, switchgrass and other crop residue materials—as the next feedstock that will generate the necessary domestic production volume to meet the aggressive renewable fuel standard.
Fractionation technology is the process of a dry grind and separation of the corn kernel components prior to fermentation. By grinding and separating beforehand, the higher food value portions of the kernel (bran) are separated and sold as high-quality food ingredients, while heavier starch components move to the fermentation process. The technology adds value to the revenue stream and quality to the byproducts (distillers grain), while reducing the overhead costs related to unnecessarily processing portions of raw materials.
Oil extraction is either placed at the beginning or the end of the production cycle. At the beginning, clean, food-grade corn oil is extracted and sold in the traditional food procurement supply chain. If extracted at the end of the production cycle, fuel-grade corn oil from the distillers grain can be used in traditional industrial processing products or non-traditional biodiesel production facilities.
Logistical Pressures
Ethanol, due to its relatively high corrosive characteristics, can’t be transported though traditional pipeline systems. As a result, the additional ethanol volume is new traffic to the rail industry, with California being the largest market. Each tanker carries approximately 30,000 gallons of ethanol. A traditional 50-million-gallon ethanol plant running at 120 percent of nameplate capacity (60 million gallons) uses approximately 2,000 tanker cars a year to distribute its production. Its primary byproduct, distillers grain, utilizes approximately 2,000 more grain cars.
Because of this long-distance traffic, non-integrated business sectors have experienced increased supply chain pressures. While legislation has been introduced to potentially fund an ethanol pipeline, it may be years before this becomes reality.
Raw Material Pressures
Additional supply chain pressure is created from the construction of renewable plants, which rely heavily on steel—especially stainless steel—because ethanol has greater corrosive characteristics than petroleum-based gasoline. It’s estimated that a single traditional 50-million-gallon ethanol plant utilizes approximately 1,000 tons of stainless steel, and, as a result, many suppliers have noted the price of stainless steel doubling over the past two years. In addition, the entire renewable fuel distribution network is lined with new stainless needs for tanks, pumps and other containers.
While the renewable fuel boom is creating a new advanced manufacturing environment, its impact will surely be felt across the manufacturing industry as new products and technologies evolve and supply chain dynamics adjust to new market economics. IBI