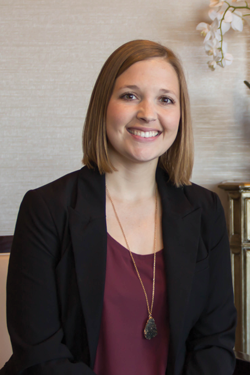
Reduce the costs associated with your waste stream.
Energized by receiving training in lean manufacturing methodologies, an engineer forms an internal team to map the value stream of her company’s key product line or processes, revealing cost- and time-saving opportunities. Feeding on the enthusiasm of her team, recommendations are made to management about the path to move forward. Management encourages the engineer to focus on eliminating traditional wastes, such as time spent waiting, inventory, and excess material or component transportation. Meanwhile, some obvious environmental and energy wastes are ignored, and along with them, the opportunities for significant savings.
E3: Economy, Energy, Environment is a concept in continuous improvement that balances the efficiencies of a company’s processes with the development of sustainable operating practices. The bottom line is that you can realize even larger savings through an optimized look at all of your key processes. By implementing process changes consistent with the E3 foundation, you can address the following challenges:
- Inability to identify less expensive, non-landfill options for waste;
- Stringent regulations for alternative waste solutions;
- Inability to separate waste streams;
- Material waste caused by ineffective processes;
- Balancing production demands with energy demands; and
- Creating a culture that looks at all waste in the facility.
When embarking on a lean continuous improvement journey, a company will almost always indirectly eliminate green-related wastes. By reducing inventory, for example, a company will inherently save on materials. Or when reducing batch sizes per a standard lean recommendation, material wastes may also be reduced because extra materials are no longer needed during changeover.
However, combining Lean (Economy) with Green (Energy and Environment) through specific waste elimination metrics will ensure that continuous improvement programs do not ignore environmental wastes such as excess electricity, discarded materials, overuse of water, etc. In addition, making green a part of continuous improvement is needed to ensure that it is not thought of as some separate program or “flavor of the day.” Creating green improvements will enhance a company’s sustainability program and result in improved efficiencies and significant savings. This ensures that the company’s machine resources, people resources, capital resources and environmental resources are utilized as effectively as possible, with minimal impact on the earth.
Beyond the environmental benefits and cost savings, the consequences of not dealing with these wastes include increased disposal costs, regulatory paperwork and fines, as well as increased costs assigned to waste materials. A lean and green approach will give manufacturers the ability to:
- Identify recycling and reuse options;
- Improve the quality of the waste stream so it can be reused internally or by another manufacturer as input; Develop efficient systems that will enable reuse or recycling waste;
- Aid in product design that can minimize the use of materials, resulting in less waste; and
- Focus efforts on how best to manage energy usage. iBi
If your company is not running lean and green, and you wish to reduce costs associated with excess processes, call IMEC at (888) 806-4632 or visit imec.org.