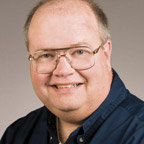
IMEC’s Monte Carlo Simulation predicts the effectiveness of future process changes.
Some call it game playing. Others may refer to it as a simulation. No matter what the name, the ability to test and validate proposed changes to processes before the first machine is moved can be a significant time and cost saver.
An IMEC client recently asked us help them do just that on processes they were developing for a new product line. We deployed the “Monte Carlo” method, which predicts potential outcomes within a complex process by running statistical models off of randomized inputs. Odds makers use the technique to model sporting events and predict which team will be favored to win a certain percentage of the time. The term “Monte Carlo” was the code name given by scientists who developed a computational method for determining the performance of the atomic bomb.
IMEC was already familiar with the processes that our client wanted to validate, having worked with their team to design the production cells, supermarkets and shop floor layouts for the new line. We decided to follow the movement of containers of product through the manufacturing process using the cycle times, setup times and flows for the new plant. We simulated a container of product by using a simple sticky note, which we moved along the process depending upon how long it took to set up and run the job. The sticky note represented parts flowing through the various manufacturing cells until they reached the supermarket as finished goods. Sales of a given product were randomized using an Excel add-on that was based on the historical sales of that product. As sales came in, the parts were withdrawn from the container, and as containers were emptied, they were sent back to the beginning process according to the Kanban rules that the client and IMEC had established. In all, more than 350 different parts were evaluated.
Among our findings, we were able to determine when product would be in stock, how well the supermarket would keep up with uneven demand, a production schedule that would fill inventory the fastest, and how to build extra inventory of 6,000 special sets of product to help introduce the new product line.
As a result of this project, IMEC is developing two new services that will appeal to a broad range of manufacturers: The first is a four-hour case study to augment our existing Lean Pull/Kanban deliverable. It will enable a manufacturer to design a Kanban system and then watch the flow on supermarket containers throughout a manufacturer’s unique process. The second service is to create highly customized simulations that manufacturers can leverage to model their own process and/or validate changes they wish to make.
These Monte Carlo simulations enabled IMEC and the client team to view and analyze key processes as a group. The interaction and discussions that resulted were extremely valuable and enabled the company to make informed decisions about how to optimize the new product line. For more on utilization of this tool, contact IMEC at info@imec.org. iBi