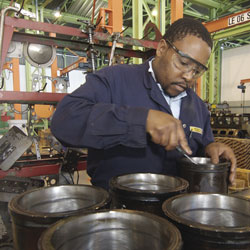
Landfilling may remain the primary method of removing waste in the United States, but consumers are becoming increasingly aware of the problems associated with shrinking landfill space and the potentially detrimental impact created by end-of-life products. As a result, a growing number of concerned citizens, consumers and corporations are looking for guidance in how to handle the excess. For a company like Caterpillar—whose core business is manufacturing—one answer lies in embracing a strategy of Extended Producer Responsibility (EPR), where companies are responsible for the impact of their products throughout their life cycles.
“We put a lot of effort and focus on supporting our products through the first life cycle and multiple life cycles thereafter,” stated Joe Allen, general manager and director of sustainable development for Caterpillar’s Remanufacturing (Reman) Division. “We really bundle that into the three Rs of reduce, reuse, and recycle to help customers achieve the best value and greatest benefit from their products.”
But how exactly does a “product recycling” program work at a company like Caterpillar? By developing a strategy and the infrastructure to support a worldwide product take-back program.
“Think about the basic example of a bottle of Coca-Cola,” Allen explained. “We used to buy a bottle for a dollar and there was a 25-cent deposit on the bottle. You bring the bottle back and you get your 25 cents back. There’s value for the producer in the Coke bottle because it can be reused or recycled into another usable product. In our business, that’s the Reman program. It’s take-back. And in our products, there’s value in the end-of-life product at the end of its life. For Caterpillar, it’s a large, closed-loop recycling mechanism on a global basis.”
By establishing a product take-back program, Caterpillar builds long-term relationships with customers through a series of product purchases and returns.
“Our remanufacturing program is based on an exchange system. Customers return a used component and receive a remanufactured replacement component with same-as-new quality, reliability and warranty in return,” said Allen. “We then use the end-of-life returns in the remanufacturing process to produce like-new remanufactured products—or better-than-new if we are able to design and implement new engineering changes into that product.”
Because Caterpillar is returning end-of-life components to same-as-new condition, they reduce waste and minimize the need for raw material to produce new parts. Through remanufacturing, nonrenewable resources are kept in circulation for multiple lifetimes—supporting the company’s goal for a zero landfill footprint by 2020.
Remanufacturing continues to be a growing business for Caterpillar. In 2007, the company took back over two billion pounds of material—that’s equal to over 56 billion aluminum cans—and today they have 17 facilities around the world dedicated to remanufacturing products.
“As customers are trying to get the best economic life out of their machines, the best way to do that is to build the machines so they’ll have multiple lives,” said Allen. “We need to produce product with multiple life cycles in mind to keep excess waste out of landfills. EPR drives us to use eco-design—or in our case, ‘Design for Reman and Design for Upgradeability.’”
When using Design for Reman, Caterpillar considers the entire product lifecycle before the design phase even begins, considering such things as type of material used and ease of disassembly for repair, remanufacture, reuse or recycle. By considering the product’s remanufacturing potential in the product design phase, Caterpillar engineers have enabled some components to be in circulation for multiple lifecycles.
According to Allen, strategically positioning the remanufacturing program on a global basis has helped Caterpillar build and continue to expand its EPR focus, including repurposing products into completely different applications than originally intended.
“We currently have a pilot project where we’re building a process to take back diesel truck engines from North America, remanufacture them into gas configurations of that engine that burn methane, package them into generator sets, and then deliver them to the developing world to help them meet their electric power needs. This is a unique effort where we can eliminate a very potent greenhouse gas and generate clean power to the developing world,” said Allen.
Caterpillar is also finding ways to expand its remanufacturing business model to help address growing environmental problems—like electronic waste.
“We’re pretty clear at Caterpillar that we want to be part of the solution, not part of the problem,” said Allen. “And, we look at our remanufacturing take-back program as one possible solution.”
By leveraging the existing business model, Caterpillar is accelerating the remanufacturing of electronic components from our machines and engines. “We’d love to have a zero e-waste footprint,” said Allen. “That’s our vision. And we’re moving in that direction fairly quickly.”
Caterpillar has seen significant business value generated by taking products back when customers have finished using them. “When you look at our remanufacturing program today, our end-of-life return rate on a global basis is at 93 percent. So for every 100 remanufactured parts we sell, we get 93 back.” That’s quite a statistic when you consider that the recycling rate in the United States is around 33 percent. iBi