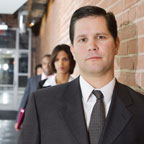
Logistics and supply-chain management issues have plagued mankind for millennia. Even the makers of the first wheels probably struggled to develop the right tools, assemble needed raw materials and maintain sufficient inventory to meet demand without impeding their mobility and flexibility.
Fast-forward to today, and you’ll find owners and executives of many mid-sized businesses struggling with those same problems, albeit with a decidedly more modern spin. Today’s business owners must strive to maintain a delicate balance between rawmaterials availability, production speed and cost and customer demand—all while struggling to compete in an increasingly global marketplace.
Consider applying some of the “lean” production principles that major automobile manufacturers made famous. As part of your mid-sized business’s logistics and supply-chain processes, these principles could boost your company’s competitiveness, efficiency and profit, according to industry experts. But, these same experts caution, before you can reap the rewards, you must be willing to rethink your company’s basic definitions of concepts such as cost, assets and inventory.
The following information can help you learn more about “lean logistics” and how you might apply this approach to your own mid-sized company.
Logistics management and supply-chain management
Logistics management and supply-chain management are often used interchangeably, although the Council of Supply Chain Management Professionals (CSCMP) defines logistics management as a subset of supply-chain management.
Logistics management, according to the CSCMP, is “that part of supply-chain management that plans, implements and controls the efficient, effective forward and reverse flow and storage of goods, services and related information between the point of origin and the point of consumption in order to meet customers’ requirements.” Supply-chain management, the council says, “encompasses the planning and management of all activities involved in sourcing and procurement, conversion and all logistics management activities.”
No matter how you define it, logistics is an enormous expenditure for U.S. companies. According to a report by CSCMP, the cost of logistics in the United States totaled $1.015 trillion in 2004, which equals 8.6 percent of the country’s gross domestic product for that year.
What does it mean to be lean?
It’s easy to become overwhelmed with the myriad complexities of logistics and supply-chain management, especially if you have a global supply chain or a large number of entry and exit points for goods and services. So it can be difficult to determine where to begin optimizing your own supply chain. However, a growing number of mid-sized companies are looking to lean principles to trim the fat and boost the speed and efficiency of their production processes.
James Womack coined the phrase “lean manufacturing” in his 1990 book, The Machine That Changed the World, which examined automobile production in Japan, the United States and Europe. However, aspects of the lean quality initiative—including cutting waste, improving throughput and eliminating errors —have been espoused by notable figures throughout history. Ben Franklin once wrote, “Buy what thou hast no need of, and ere long thou shalt sell thy necessaries.” And Henry Ford, arguably the father of lean logistics, summed it up: “The longer an article is in the process of manufacture and the more it is moved about, the greater is the ultimate cost.”
Lean principles extend far beyond the automotive arena and may apply to any repetitive process across all industries, including manufacturing and software development.
Lean and Six Sigma
In recent years, logistics experts have discovered that marrying the basic tenets of lean logistics with the statistical rigor of other quality initiatives such as Six Sigma creates a union ideal for reliably calculating a product’s total cost and fine-tuning supply-chain complexities.
Six Sigma’s name comes, in part, from the lowercase Greek letter sigma, which represents standard deviation. It refers to the idea that, if you have six standard deviations between the mean of a process and the nearest specification limit, you will make no items that exceed the specifications.
Six Sigma’s statistical firepower has helped lean-logistics practitioners pinpoint areas that need to be leaner which might otherwise have gone unnoticed.
Road map to success
What do you need to do to apply lean logistics to your mid-sized company? What benefits or risks might you encounter? Here are some steps to get started with lean logistics.
Step 1: Educate yourself and your employees.
While you may choose to hire a consultant or take a seminar to help you get started on lean logistics, accomplishing significant change in your organization means educating and involving everybody in the company, not just a select few. Make sure all your employees know the basics of lean logistics and how they can help make it a success.
Step 2: Look at the big picture.
Many companies purchase raw materials from the vendor with the lowest bid. Lean logistics, with the help of Six Sigma or other statistical tools, enables companies to see the total cost of using a specific vendor. How many distribution points do the materials pass through before getting to their destination? Do the materials come packaged as a productionline- ready “ship set” to speed the product’s throughput? Precise statistical analysis can help clarify the big picture. You might find a practice that appears to be saving money actually costs more in the long run.
Inventory is another area where experts advise you to take the broad view. Whereas many businesses look at their standing inventory as an asset to accumulate and store, lean-logistics experts advise you to think of it instead as insurance — a necessary expense you should purchase in the smallest quantity required to keep your production line running. Experts say forming relationships with vendors who can get you what you want, when you want it, will ultimately reduce waste, decrease costs and boost your bottom line.
Step 3: Start with the “low-hanging fruit.”
No matter how committed you are to the principles of lean logistics, you shouldn’t aim to implement it everywhere at once. In fact, attempting to do so could significantly limit your overall chance of success. Instead, pick a single product or product family and diagram every aspect of that process from quote to cash, looking for any examples of redundancy or waste.
Next, look for the “low-hanging fruit” in the process—easy targets that will give you practice with your newfound tools and concepts, and help prove to skeptics the real and positive benefits of lean logistics. IBI
Fast-forward to today, and you’ll find owners and executives of many mid-sized businesses struggling with those same problems, albeit with a decidedly more modern spin. Today’s business owners must strive to maintain a delicate balance between rawmaterials availability, production speed and cost and customer demand—all while struggling to compete in an increasingly global marketplace.
Consider applying some of the “lean” production principles that major automobile manufacturers made famous. As part of your mid-sized business’s logistics and supply-chain processes, these principles could boost your company’s competitiveness, efficiency and profit, according to industry experts. But, these same experts caution, before you can reap the rewards, you must be willing to rethink your company’s basic definitions of concepts such as cost, assets and inventory.
The following information can help you learn more about “lean logistics” and how you might apply this approach to your own mid-sized company.
Logistics management and supply-chain management
Logistics management and supply-chain management are often used interchangeably, although the Council of Supply Chain Management Professionals (CSCMP) defines logistics management as a subset of supply-chain management.
Logistics management, according to the CSCMP, is “that part of supply-chain management that plans, implements and controls the efficient, effective forward and reverse flow and storage of goods, services and related information between the point of origin and the point of consumption in order to meet customers’ requirements.” Supply-chain management, the council says, “encompasses the planning and management of all activities involved in sourcing and procurement, conversion and all logistics management activities.”
No matter how you define it, logistics is an enormous expenditure for U.S. companies. According to a report by CSCMP, the cost of logistics in the United States totaled $1.015 trillion in 2004, which equals 8.6 percent of the country’s gross domestic product for that year.
What does it mean to be lean?
It’s easy to become overwhelmed with the myriad complexities of logistics and supply-chain management, especially if you have a global supply chain or a large number of entry and exit points for goods and services. So it can be difficult to determine where to begin optimizing your own supply chain. However, a growing number of mid-sized companies are looking to lean principles to trim the fat and boost the speed and efficiency of their production processes.
James Womack coined the phrase “lean manufacturing” in his 1990 book, The Machine That Changed the World, which examined automobile production in Japan, the United States and Europe. However, aspects of the lean quality initiative—including cutting waste, improving throughput and eliminating errors —have been espoused by notable figures throughout history. Ben Franklin once wrote, “Buy what thou hast no need of, and ere long thou shalt sell thy necessaries.” And Henry Ford, arguably the father of lean logistics, summed it up: “The longer an article is in the process of manufacture and the more it is moved about, the greater is the ultimate cost.”
Lean principles extend far beyond the automotive arena and may apply to any repetitive process across all industries, including manufacturing and software development.
Lean and Six Sigma
In recent years, logistics experts have discovered that marrying the basic tenets of lean logistics with the statistical rigor of other quality initiatives such as Six Sigma creates a union ideal for reliably calculating a product’s total cost and fine-tuning supply-chain complexities.
Six Sigma’s name comes, in part, from the lowercase Greek letter sigma, which represents standard deviation. It refers to the idea that, if you have six standard deviations between the mean of a process and the nearest specification limit, you will make no items that exceed the specifications.
Six Sigma’s statistical firepower has helped lean-logistics practitioners pinpoint areas that need to be leaner which might otherwise have gone unnoticed.
Road map to success
What do you need to do to apply lean logistics to your mid-sized company? What benefits or risks might you encounter? Here are some steps to get started with lean logistics.
Step 1: Educate yourself and your employees.
While you may choose to hire a consultant or take a seminar to help you get started on lean logistics, accomplishing significant change in your organization means educating and involving everybody in the company, not just a select few. Make sure all your employees know the basics of lean logistics and how they can help make it a success.
Step 2: Look at the big picture.
Many companies purchase raw materials from the vendor with the lowest bid. Lean logistics, with the help of Six Sigma or other statistical tools, enables companies to see the total cost of using a specific vendor. How many distribution points do the materials pass through before getting to their destination? Do the materials come packaged as a productionline- ready “ship set” to speed the product’s throughput? Precise statistical analysis can help clarify the big picture. You might find a practice that appears to be saving money actually costs more in the long run.
Inventory is another area where experts advise you to take the broad view. Whereas many businesses look at their standing inventory as an asset to accumulate and store, lean-logistics experts advise you to think of it instead as insurance — a necessary expense you should purchase in the smallest quantity required to keep your production line running. Experts say forming relationships with vendors who can get you what you want, when you want it, will ultimately reduce waste, decrease costs and boost your bottom line.
Step 3: Start with the “low-hanging fruit.”
No matter how committed you are to the principles of lean logistics, you shouldn’t aim to implement it everywhere at once. In fact, attempting to do so could significantly limit your overall chance of success. Instead, pick a single product or product family and diagram every aspect of that process from quote to cash, looking for any examples of redundancy or waste.
Next, look for the “low-hanging fruit” in the process—easy targets that will give you practice with your newfound tools and concepts, and help prove to skeptics the real and positive benefits of lean logistics. IBI