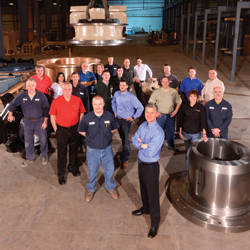
Training, education and a shift in perception may be just what it takes to fill the talent gap in the local workforce.
Bud Grieves' philosophy is to train his workforce wherever an opportunity arises. The owner of the Mark Twain Hotel in Peoria has not only encouraged his staff to improve themselves, he offers scholarships to Illinois Central College for that purpose. "I obviously think it is very important if we can offer on-the-job training,” Grieves said. “One of our practices is to bring someone in as an intern to learn the various jobs in the hotel.”
Last summer, for instance, a student from Western Illinois University worked at the hotel and was given a firsthand look at its functioning. General Manager Naomi Shea said this practice is as old as the hotel itself. "It's just part of the hiring incentives," Shea said. "We will offer people who have been with us for at least a year and are in good standing a scholarship to ICC for as long as they are employed at the hotel."
An ICC graduate herself, Shea is a strong supporter of the college and believes it offers some of the best training available for the workforce. "You can go there and find just about anything you want to learn to prepare yourself for employment," she said.
The scholarship offer is also extended to the spouses and children of Mark Twain employees. Staff members who accept the offer of self-improvement sometimes move on to a four-year college with the blessing of their employer. "Our only requirement is that they write a letter to thank Bud for the opportunity," Shea said. She believes Grieves has received at least 30 such letters over the years.
Workforce Is the Foundation
Preparing the regional workforce in central Illinois is a key component of the strategy being developed through the new regional economic development project known as Focus Forward CI. Mike Everett, president of the West Central Illinois Labor Council, said he’s seen a positive paradigm shift over the past few months, as the region recognizes that the workforce is the foundation for a successful economy.
“I was skeptical at first, but I believe we may have found a better approach to continuous economic development,” he said. “We used to chase employers and chase jobs, but in the long term, the focus should be on the workforce and making this an attractive place to work and live, and that will attract opportunities.”
The Boston Consulting Group, a leading management consulting firm, estimates that U.S. employers currently lack 80,000 to 100,000 highly skilled manufacturing workers. It also warns of a shortage of 875,000 machinists, welders, industrial engineers and mechanics by 2020—especially as more jobs come back to the U.S. and the economy returns to a more historically typical rate of growth.
Manufacturers are reporting a gap in the talent they need to continue to grow, caused by both retirements in the current workforce, as well as a general lack of interest or encouragement of new individuals to go into manufacturing as a career. And these shortages in skilled production jobs are precluding businesses’ ability to expand and drive innovation.
Connecting the Resources
Doug Parsons, CEO of Excel Foundry & Machine Inc. in Pekin, chairs the FFCI Workforce Action group, which is collecting data and working to understand the region’s strengths and weaknesses in order to develop a comprehensive strategy that will address the workforce issue and put central Illinois on the path to achieving FFCI’s goals by 2018.
"Over the past couple months, we have gone through a fairly extensive process of identifying and inventorying all the various workforce development resources throughout the region,” Parsons said. “I have been amazed at the abundance of resources available, but I have been equally amazed at how fragmented and disconnected all these resources are from each other. Our mission is to build effective and efficient conduits for job-seekers to understand the pathways to immediate employment opportunities."
Area leaders have also noted training facilities and tools that aren’t being used or leveraged to their full potential. Excel is already working to address these issues through its involvement in the annual Manufacturing Expo at the Civic Center, which engages high school students and directly in their schools. The firm has also partnered with MidWest Central High School in Manito, recently placing a machine tool in the school.
“One of the many challenges educators have is coming up with the resources to equip themselves to do what we’re asking them to do,” Parsons said. “Our challenge is getting the employers (the real job creators) to engage and become partners with the educators. At the end of the day, it’s only going to hurt us if we don’t have the skilled workers we need to grow.”
Everett agrees, saying the responsibility for education is not just on schools and training programs, but on employers themselves. The unionized construction industry in this region spends millions of dollars each year on training, in addition to handling its own recruitment and job placement.
Onshoring: An Opportunity
Over the next 10 years, millions of manufacturing jobs will return to the U.S. In an interview with H. Wayne Wilson on WTVP-TV in January, Frank Knott of ViTAL Economy, the consultant leading the regional effort, attributed three main reasons for jobs returning to the U.S.:
- Cost of energy—to ship a product is expensive
- Foreign wages are increasing
- Companies are rethinking the total risk of having manufacturing overseas, along with the competitiveness of the American workforce.
With the return of these manufacturing jobs, there’s a need to demonstrate that they can translate into good careers. Among FFCI’s goals is not only an increase in the number of regional jobs, but also the base salaries for those jobs. Goals specific to workforce development include creating 13,190 new jobs across the region (1,319 new jobs at $53,715/year and 11,841 new jobs at $48,832/year), improving the pay rate of more than 19,000 existing jobs by $5,000/year, and ramping up education attainment of bachelor and graduate degrees by 2,300 from the current 2012 estimate of 68,719.
ViTAL Economy recommendations that might be embraced in the coming months or years include a leadership training program, small business incubator and numerous centers of excellence. (A data center of excellence is a centralized Internet site that allows economic development professionals and businesses access to data pertaining to economic development.)
A final element that cannot be ignored is the negative perception of a career in manufacturing, says Parsons. “Successful manufacturing companies today rely heavily on forward-thinking, team-working problem solvers who are utilizing advanced machine tools, computers and robotics… I think a lot of people are surprised when they learn how dramatically the environment in manufacturing has changed in just the last 10 years.” iBi