More Than Just Certification
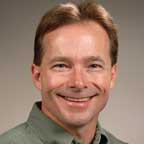
Then, reality sets in. Like many companies, they begin to realize many of their documented procedures are not being followed or maintained. The information and data being collected is rarely looked at or analyzed. The certification is fast becoming viewed as a cost of doing business, rather than a roadmap that drives continuous improvement. The management team abandons the quality management system. Internal audits are discontinued, management reviews cease, and equipment calibrations are ignored. A once-promising QMS has crashed and burned!
This scenario plays out every week in manufacturing firms throughout Illinois. How can these companies re-invent and re-energize their quality systems?
The one constant in an effective quality management system is leadership involvement. At IMEC, we often start each journey with an ISO gap analysis to show the client team where the real opportunities for improvement lie, and what it will take to make the improvements and sustain them. Basic training is provided on the essentials of a quality management system to help leadership teams gain a clear understanding of the ISO standard. It is simply not enough to put quality tools (statistical process control, advanced product quality planning, 6 Sigma, etc.) in place. A functioning QMS requires management discipline and a real commitment to success.
The standard itself is helping. The evolution of ISO 9001:1999 to the current ISO 9001:2008 has changed the focus from prescriptive documentation to understanding and improving processes. As the project implementation progresses, it is often rewarding to see the culture changes taking place as the team gains an understanding of the QMS and how it can really provide benefits to their company. These lessons can be applied to any company that feels that it is not "getting the value" from its investment in a quality management system.
Manufacturers face many competitive challenges today. Delivering impeccable quality, on-time and on-budget, is the price of entry into the game. It is expected. What separates the winners, however, is the commitment to service, to exceed customer expectations, and practice the discipline that makes a working QMS a part of everyday business. iBi