Quality Engineering
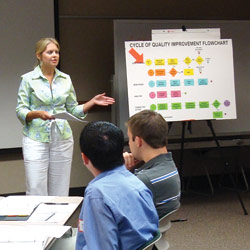
“Quality” in engineering (real or perceived) is an essential aspect of a successful engineering consulting firm. Some quality “gurus” (Deming, Juran, Crosby, etc.) say that quality is not a destination, but rather a journey with no end. CMT embraces this view and has been on this journey for the past 16 years. This is our story.
The simple acts of turning on a water faucet, switching on a light or crossing a bridge do not usually cause one to consider the standard of care or level of detail required to engineer these daily conveniences. Indeed, the practice of civil engineering touches our day-to-day routine in multiple ways. The level of detail involved in engineering a set of plans and specifications for a civil project can be significant. Errors or omissions can be costly. The increased pressure to deliver services at lower costs and on faster schedules makes the issue of quality management one of prime importance.
Crawford, Murphy & Tilly, Inc. (CMT) began its formal “quality” journey back in 1993 when its leadership made the commitment to deploy a firm-wide Total Quality Management (TQM) system. The challenge was to adapt TQM principles that had primarily originated in the manufacturing industry to a service firm, and specifically, an engineering service firm.
After about a year of planning, organization and in-house training, the initial TQM-based Quality Management System (QMS) was rolled out company-wide. Assimilating the firm’s culture to the new system has been an ongoing evolutionary process and one that is formally reevaluated every five years. The first five-year retooling changed the initial stand-alone, activity-based QMS to what is now a more integrated, results-based Continuous Improvement Initiative (CI Initiative).
CMT’s CI Initiative is founded on a set of various core concepts and managing elements that have remained consistent over the years, the full content of which would be beyond the scope of this article. Looking back on the journey, there are some key principles of the initiative that have been instrumental in its success. Integrating these principles into our business operations has enabled the consistent delivery of quality engineering services and projects to our clients.
Leadership from the Top
Consistent quality does not happen by accident—it can only be delivered with intentional and committed leadership from top management. CMT’s CI Initiative is led by a 21-member Continuous Improvement Management Team (CIMT), which is chaired by the CEO and managed by a senior-level officer who functions as the firm’s CI manager.
In addition to the firm’s top officers and business unit directors, “CI Leaders” are selected from each operational unit and serve on a rotational basis to “champion” continuous improvement initiatives within their respective units. These positions also provide leadership opportunities for staff not typically in formal management positions.
The CIMT plays a key role in reevaluating the performance of the system on an annual basis. CI operations are also an agenda item in regularly scheduled operational unit and Board of Director meetings.
Firm-Wide Focus on Core Business Processes
CMT’s core business is project delivery. TQM principles are incorporated into project delivery in several ways. Early on in the process, CMT developed and documented a formal project management system which provides project managers/engineers detailed guidelines and best practices for quality project delivery. The Project Management Manual provides defect-prevention techniques such as project kick-off meetings, constructability reviews, project management checklists, and recommended project execution processes.
On individual projects, project managers prepare a Project Quality Assurance Plan (QAP). The QAP includes an independent review of engineering calculations and deliverables.
To ensure continuous improvement is a company-wide emphasis, CMT’s CI Initiative includes the requirement that all operating units complete Continuous Improvement Projects (CIPs) each year. A CIP is intended to eliminate defects or improve work processes. Every employee has the opportunity to be involved in the CIP process.
Many of the opportunities for improvement projects come from CMT’s annual Lessons Learned Program, in which each operating unit conducts a two-hour “lessons learned” session to recap and learn from those project and operational experiences during the past year, both positive and negative. Since the CIP program began in 1995, 276 CIPs have been completed.
Customer Feedback is Essential
The perceptions of the firm’s clients and employees are routinely measured at CMT. Ultimately, it is the customer (client) who defines quality. The firm’s Client Satisfaction Improvement Process (CSIP) is a program in which senior managers meet with the top 40 clients approximately every two to three years with a two-fold purpose: 1) to ask for input on how CMT can better serve their engineering/project delivery needs; and 2) to obtain an overall evaluation of our consulting services for the prior two- to three-year period. Over the past 14 years, more than 230 CSIP visits have been made and over 350 evaluation questionnaires have been received. Consistent receipt of eight, nine and 10 ratings provides us an objective measure, which proves our quality journey is worth the effort. When individuals or project teams are singled out for praise, those comments are publicly posted on our “Quality Matters” bulletin board.
In addition to external feedback, management also seeks feedback from our internal customers via CMT’s annual Employee Opinion Survey. The results of this survey have improved from 3.4 (on a 5-point scale) in 1994 to 4.45 in 2008. This improvement in employee satisfaction was reflected in CMT being honored by Civil Engineering News in 2008 as one of the “Top Ten Mid-Sized Engineering Firms to Work For.”
Quality Recognition
In order to reinforce CMT’s commitment to quality performance and quality improvement, the firm developed a formal recognition system that recognizes employees for support of continuous improvement and performance. The process culminates in an annual recognition celebration where employees are honored publicly and recognized monetarily for achievements in either engineering project delivery or internal business process enhancements. Evaluation factors for recognition include the application of Continuous Improvement principles.
Overall, the CI Initiative has served CMT well over the past 15-plus years in helping to provide quality services and deliverables. We plan to continue our Continuous Improvement journey indefinitely with the expectation that an improved firm is always possible and also necessary. iBi
Warren Knoles, P.E. is the COO and director of Engineering for Crawford, Murphy & Tilly, Inc., and the primary developer of the firm’s quality program.