Continuous Quality Improvement
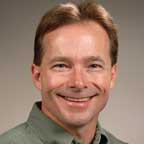
Over the years, operating and management strategies have taken on new names, new packaging and have even become their own “fads” within industries. Who can forget Quality Circles in the late '70s or TQM in the 1980s? Today, there’s TPM, TPS, Lean Manufacturing, 6 Sigma, Training Within Industry and Value Engineering. There’s ISO, TS, QS, AS 9100, SPC, PPAP, APQP, fishbones, Paretos, scatters and hundreds more.
Regardless of what buzzwords are attached, most companies want to deliver products of impeccable quality, on time, at costs that will generate the highest profit margins. If the pursuit of these goals is viewed as a short-term strategy with a defined lifespan, it doesn’t fit the most appropriate and impactful name of all: Continuous Improvement.
Local companies I have visited often tell me their lean manufacturing deployments are stalled. Some leaders say they’ve done “all they can.” Still others have invested considerable dollars and time in a continuous improvement methodology—6 Sigma, for instance—but are not seeing the return on their investment.
Integrating Lean Manufacturing, 6 Sigma and other continuous improvement strategies is actually a simple concept. If you consider all the tools these methods have to offer and select the right one for the task at hand, it really doesn’t matter what you call your strategy…as long as you have one.
Get the best out of both methodsBy integrating Lean and 6 Sigma, companies are able to tackle problems more effectively. Simply put, lean tools are a good choice for eliminating waste. 6 Sigma works best when a company needs to tackle a specific problem and minimize variation in a process.
These processes are not mutually exclusive. In fact, if you deploy 6 Sigma alone, you may end up spending months fixing a process that in itself could be wasteful. Conversely, if you only implement Lean, you may never get to the root cause of specific problems that, if corrected, could transform your quality or cost structures. By combining Lean and 6 Sigma, you have the opportunity to:
- Address all key processes
- Seamlessly integrate waste removal, time and variability reduction, and increased productivity
- Deliver products more quickly with exceptional quality
- Impact business improvements rapidly
- Achieve a competitive edge in the market.
Where to begin
When trying to rationalize the two approaches, think of it this way: When you build a home, you have a blueprint. Each project calls for a specific set of tools and guidelines to ensure that sections of the structure are being built with utmost quality and safety. Yet at the same time, you are following a process to build the home in the most timely and cost effective fashion.
The same analogy holds true in your business. You can’t select your tools until you have a defined set of objectives for your projects. Value Stream Mapping, for example, is one of the foundations of a Lean Enterprise. It allows you to look at every step in the operational process and identify the actions that do and do not add value to the end customer. Using this roadmap, you’re able to identify performance gaps, define improvement projects, charter improvement teams and select the right tools for closing the gaps. One such tool might be 6 Sigma.
Too often, companies see Lean and 6 Sigma as distinctly different initiatives. Without integrating the two programs, these implementations can compete for resources and end up limiting the success of either. A unified approach will conserve valuable company resources and achieve maximum results at a more rapid rate. iBi