Peoria Robotics
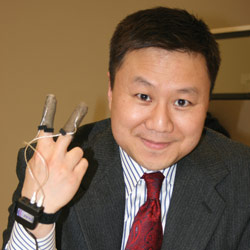
Dr. Andy Chiou is a vascular surgeon and partner at Peoria Surgical Group, faculty member at the University of Illinois College of Medicine at Peoria, and an adjunct professor of engineering and technology at Bradley University. A former lieutenant colonel in the United States Air Force, Chiou is a self-described “homegrown product of Peoria.”
Chiou is also one of the co-founders of Peoria Robotics, a research group that is working on a system to provide more realistic simulations for the purpose of training medical professionals, with additional applications in other fields. In February 2009, Peoria Robotics announced it had received an $850,000 grant from the United States Army to develop this medical training simulator.
Describe the initial impetus for Peoria Robotics. What were the circumstances under which the group was formed?
This is really a great convergence of what is naturally homegrown from Peoria. It was part of the original [Peoria NEXT] Discovery Forum series, an innovation forum in July 2004. It was a half-day of presentations from Cat engineers, scientists, folks from the Ag Lab and the medical sector, and others. I had actually just moved back to Peoria the week before, from Texas.
I listened to these wonderful presentations, and they were talking about a lot of the components we are employing today, [such as] robotics and hydraulics. At the end of the day, I said, “I am from Peoria, and I just moved back last week. I don’t know exactly where this could go, but I think there are wonderful possibilities, at least in medical applications, that we can work on quickly.” At the end of the conference, we all met—a couple of engineers from Caterpillar, and some folks from Bradley, including John Engdahl, who is still with us on the project. And we asked, “What should we do now?” Since then, we have met about every two to three weeks.
The first thing we did was apply for a grant from Peoria NEXT. We got shot down initially, but it was a good exercise. The next thing we did was consider a research center of excellence on robotics, which we put together in late 2004, early 2005. Then we began to look into a viable project to present as a potential research appropriation. We were going to ask for an earmark to be placed in the Army’s Advanced Research Center, and from there we would have to apply for the competitive grant. So there had to be money for this type of project, and then we had to put together a project that would qualify. We met with Congressman Ray LaHood in 2005, and we met [Senator Dick] Durbin, and [then-Senator Barack] Obama. All of them really liked the idea, but that year [Hurricane] Katrina hit and the Iraq war was going on, so there was no money.
We continued to meet every month. This idea of a military grant was becoming clearer, and we looked at what would be the best use of research dollars. Why not work on something that could potentially help in the field, in combat? If your buddy just got shot or hit with an IED [improvised explosive device], what do I need to look for? So we came up with the idea of creating something that would use haptic palpation, when you can feel something changing and moving under your fingertips. You could sense a change in density, temperature, or vibration, and we could make a programmable model that would change size and shape on command.
You can then train for something that you wouldn’t see often, but when you did see it, you would be prepared. So you might say, “That’s a hematoma”—because you’ve run through 500 simulations and know it like the back of your hand; it’s become second nature. When the bullets are falling, you have to fall back on training—that’s what they teach in the military, and that’s what they teach in medical school. A-B-C—airway, breathing, circulation—that’s what we teach the surgical residents and EMTs. There’s a basic educational paradigm there.
The second time, we made a more robust, practical proposal and asked for one million dollars for the research component, but we also looked at the economic development aspect. We asked to work with a university, in this case, Bradley University, and eventually spin off a corporation when appropriate, a Peoria-based, homegrown corporation. This resonated nicely with the same people we presented to again—Obama, Durbin, LaHood.
The second time around, I remember very clearly, Senator Durbin asked, “Is this applicable and something you can get going in a reasonable time?” We said yes, and he worked with Ray LaHood to get it through Congress as part of the defense appropriations bill. That is the grant we have today. This was in 2006—we got the grant dollars by 2008. (They were 2007 dollars that finally came in 2008 because it took that long to get through the system.) We have asked again, and we have a portion of 2008 appropriations that we would like to compete for this year, to continue this project even further. Right now, we have about 2.5 years of funding, and we would like to add on funding that would add another 1.5 to two years.
The point is that we do the groundwork and employ the people here. One of our engineers, Justin Saboury, is from Peoria—he went to Richwoods High School and Bradley University. Our intent is to hire locally. Our technology and resources can be transported—but we want our people to be based here.
So when this started, we ran it through Bradley University, one of the largest outside grants that Bradley has ever received. Dr. John Engdahl is a principal investigator, and there are five co-investigators—lots of folks from different fields working on this. We’ve hired two engineers to work on the proof of concept, and we figure this year and into next year, we will be working on that.
The following years, we will work on actual prototype models, and all along the way, we are looking at intellectual property (IP) and patents. We hope to take this work on the proof of concept and gain enough intellectual property to take to market. Meaning, pull this IP together, and work with a partner—whether it be a Microsoft or a surgical robotics company—and say: What is it that our intellectual property can do to help your product? How do we partner and develop it?
Describe how you are using new technologies and refining existing technologies to make them more useful.
When we started this project in 2004, many of the technologies now on the shelf were not readily available. One of the early prototypes is using the infrared sensors in the Nintendo Wii for tracking. Those components might have cost tens of thousands of dollars in 2004, and even more to customize them to your needs. Today, there are millions of these units out there, but they are used in such rudimentary ways—their full abilities aren’t utilized. For example, the Wii uses two-dimensional tracking, and we are adding a third dimension to it, and potentially a fourth dimension—that being time.
The accuracy can be brought down to almost the millimeter level. So it isn’t just targeting your crossbow to hit a target in a battle game, you can bring this broadly available technology to use for something much more serious than entertainment. We are using everything available to us and adapting as we go, because technology in every field turns so quickly. You can’t say, “Here’s our technology in 2009,” because in 2010 somebody scooped you. You need to be nimble enough to leapfrog that and say, no problem—we didn’t put all of our eggs in that one basket of technology.
Our strength is in the collaboration of electrical and mechanical engineers, surgeons, nuclear physicists, computer scientists and material scientists, when you put everybody in a room and take down the barriers. The beauty of Peoria is that it is much different than if we were in Boston, and one person was at MIT and one was at Harvard. You would think that collaboration would yield tremendous output, but the reality is there are so many barriers. Yes, they can talk, but can they innovate together? They don’t necessarily have the agreements that allow them to do that, and we do.
That’s the beauty of what has happened with Peoria NEXT. We have institutional agreements that allow people from Bradley, Caterpillar, the medical school, the Ag Lab and the private sector, to talk to each other. We don’t have the same walls—we can be small and nimble and innovate just as quickly with the appropriate amount of seed money and a little bit of community backing.
Now we have cheaper sensor technology that allows us to measure differences in force applied. So what if you took hardware that is available now—and wasn’t five or 10 years ago—and utilize it with better software and touch screens that allow you to measure the depth and pressure by which you are pushing down? Our focus is developing a better medical simulator, and the premise behind it is technology that allows us to measure pressure and location, and give force feedback.
All along the way, we are going to have hardware and software developments that can be used in other applications. So when we talk about something esoteric like a hematoma simulator—we are also talking about training medical students on how to detect a breast cancer lump or how to detect prostate cancer earlier. This is much different from the current, rudimentary models we have, such as a marble fixed in some Styrofoam.
And the applications become much broader than medicine. There is innovation across the manufacturing, electronics and entertainment spectrums, as well as heavy machinery and the automotive field. Peoria Robotics is not a medical company or a manufacturing company. It is purely an innovation center, and eventually an innovation company.Describe the vision for the end product of this research.
This grant is to be very focused on measuring the movements of an expert user, much like what you have in fighter pilot simulations—the range and parameters using a particular piece of instrumentation, whether it’s a medical simulator or a jet fighter plane. We would then measure what expert personnel would apply for pressure to examine a particular area of the human body, record that measurement, and create…what we will call a “magic box.” (I don’t want to get into too much detail because much of that is what we will develop.)
So, this “magic box” can reproduce a mass, which can double in size over time, or change in depth within the box. The student is being tested to find the mass and tell us whether it is expanding, contracting, or pulsating, and where it is located. We are then able to measure the pressure and where it is applied, and use it as testing tool. This takes the subjectivity out of medical testing, judging them purely on objective data. Are they pushing hard enough to the human limit of detection in finding a mass in an artificial body, or are they faking it and just telling you they are feeling it? We know the measure of pressure when the human body can detect something—so you could call it a “BS meter.” If they tell us they feel it but they can’t physically have felt it, we would know.
By taking the subjective element out and adding the feel, texture, temperature and changing aspects within the human body, we add realism back in. That will add more confidence to patient safety and the entire training model.
What are the success indicators along the way?
Some of the benchmarks would be finding successful systems that are then implemented and developing data sets that are reproducible. That will allow us to take it to the next step, once we prove that what we see and feel and what forces we are applying are measurable and repeatable, then we can start looking at developing the box.
What are the concrete applications to servicemen and women in the field?
You’re in Iraq, part of a convoy, an IED explodes. The Humvee rolls over multiple times, there’s shrapnel all over the place, your buddy is injured and unconscious. You take them to the field hospital but you’re not sure what’s wrong with them. It’s obvious, when someone gets shot and they’re bleeding, where their injury is. It’s not obvious when there’s shrapnel all over the place, and there was a blunt injury from a rollover vehicle.
So now in that field hospital, a medic who has gone through this training would know how to palpate, or feel for a hematoma—an area of internal bleeding in the body. Before, we relied on a CAT scan, but you don’t have a CAT scan at every station in the battle zone; you have to rely on human ability and the ability to feel. They may detect this early, and they would know to triage that injured soldier differently. That’s where we think we can help save lives.
How did your service in the Air Force help you formulate this concept?
I served on four surgical teams [in the Air Force]—five-person surgical teams in which we actually carry field hospitals on our backs. Everything is portable—portable operating tables and equipment, portable lights, portable everything. So in a snap situation, you could be dropped into the field, operate, and save the life of a Special Forces soldier. That experience was very helpful.
A lot of what we did was prepare for war by helping out with humanitarian disasters. We served around the world after tsunamis and hurricanes, both international and domestic. So every year, we were training; we would pack up and ship somewhere and prepare, prepare, prepare, in real-world situations. That’s the experience I’m bringing back to illustrate the real-world needs of what we want to create and how we can help save a life.So, the way that this has been presented is that there is a glove-like device and a box. Is that accurate?
Yes, there’s a glove that uses sensor technologies and does tracking and measurement. The box may initially be a simple box with items in it that are premeasured, with known densities. It may eventually be able to change internal shape.
Like a holograph?
The holograph will be a few generations ahead, but if we were to dream what it might look like five or 10 years from now, holographic technology with biohaptic feedback would be ideal. If we were to take this to an absolute limit, I guess it would be the holodeck in Star Trek. You walk in, ask the computer to program in X,Y and Z battlefield scenario, and it is created around you. You wear a suit that replicates what you should be feeling as you hit or touch something.
Or there’s an entire virtual human being on the operating table…
Exactly. Once you have that ability, you can translate it to current robotic surgical technology that allows you to operate on someone 10,000 miles in the sky, in a desolate space situation like a mission to Mars, or 3,000 feet under the water in a submerged nuclear submarine.
On the civilian side, we could do remote surgery in rural areas where they don’t have a full-time surgeon, but there are technicians. A surgeon in Peoria could perform an appendectomy on a patient in Alaska. This means you could have the same quality of care as in a large city, and no issue with access. Also, the cost of care—can you imagine if I could operate in five cities at once? That would be incredibly efficient.
Were you a science fiction fan growing up?
Absolutely, how could you not be and do what we are doing today? Part of the aspects of science fiction that always bothered me, though, were that you had high-level dream technologies, and then you would have buttons with blinking lights. So you would have things that were complete mismatches in time, and in a way, that’s kind of where we are always stuck: you have rudimentary things you want to take to the next level.
We always want to look at leapfrog technologies, so, for example, instead of laying miles of cable to develop telecommunications in a third-world country, you can go wireless—those are leapfrog technologies. They exist now but they didn’t exist 50 years ago.
We want to add human value to what we are doing. We want to come to practical application rapidly. We don’t want to get lost in the basic science; we want to rapidly transform the technology and make it usable for people in broad-based applications.
What is the future outlook for innovation in central Illinois?
When I dream about the future, one of the things we look at locally is how to diversify and grow our economy. If you don’t home-grow it, you likely won’t keep it. The guys we hire are from here, their families are here, and they will likely stay here afterwards. So the employment is largely central Illinois-based, and because of that, we don’t think this is something that could easily be moved. So, if you took a vote to see if anyone wanted to move to Silicon Valley, very few of us would say “yes.” With technology today, what would be the reason for us to move out there? As we look at the future, we hope to have a series of viable spin-off companies that will take technology as their cornerstone and package it for partnerships that will provide better products for those partners, and provide the ability for us to hire locally.
High-tech companies need engineers, scientists, researchers and doctors. What about the kids who don’t go to college, but used to be able to support their families working on the line in a manufacturing plant?
That is very salient and germane to this. We have to get out of the shell of how we think today. When you say, what about the kid who wants to go into the line job at Caterpillar that doesn’t exist anymore, I would say you are thinking about 1970 and 1980. The kid who graduates today—even if they barely graduate or don’t have the best grades—they have more exposure to technology than you can imagine. They can run circles around most of us as far as how to use your PDA, cell phone, text message, etc.
I think with the immersion in technology that exists today, even in grade school with smart-boards and computers in every room…you may not come out a valedictorian but you should come out with a skill set that will allow you to work in a technical environment far different than 30 years ago. We don’t necessarily have those jobs anymore, but who’s to say your C-student doesn’t become a programmer who works on the program line? So you have to reassess it. Maybe it’s not your blue-collar line anymore—it’s a white-collar line, providing one basic knowledge set in a long supply chain of what’s needed to develop technology. Maybe they’re not the best at calculus, but they can write code.
How do they learn this? Kids pick it up—it’s amazing at what age you learn this now. They may learn it in 5th, 6th, 7th grade…and be a great programmer by high school. Maybe you drop out of high school, but you still have a skill set. When you look at what we do in public education today, we have to infuse technology.
Home Ec is no longer just Home Ec. It is using Google to its best limits, being able to search databases you were never able to search before. You used to have to go to the library to get that data set, and now it’s available wirelessly. A lot of that is taught on the street, near the locker, in the lunchrooms. How do we formalize that? Teaching calculus should no longer just be teaching calculus, it should be calculus and rudimentary programming. Geometry, same thing, chemistry…how does it go into material science? We have to refocus all of these things.
When you have the trades wanting to help with a trade school, what might happen to the restructuring at Manual? What do they still need to learn? Accessing wireless technologies; buying and logistics supply chains; if they are going to be a contractor or subcontractor, how to find the best prices for materials, where to get it, how to look it up. To me, that’s technology that’s broad based, and you don’t just apply it in manufacturing, you can apply that in the operating room.
So however you slice it, we are all knowledge workers.
We have to be. We are no longer this highly separated state between blue collar and white collar, we are all a blend. In the operating room, I may have someone who barely graduated from high school, but finished a surgical technologist program, which is very difficult, and they have a wonderful knowledge base of new technologies in the operating room.
This is probably taboo coming from a guy like me, who’s gone through 35 years of education, with advanced degree upon advanced degree, but I think higher education has to prove its value to society, and show that it does give added value. It also puts a lot of pressure on public education at the elementary and high school levels.
It’s not like we are creating things that don’t exist, these things already exist out there. It’s turning on the TV to the Discovery Channel, and these wonderful shows that we didn’t have access to before. Now you have webinars and webcasts. It’s not the same situation now—we really are a different society. Where’s blue collar, where’s white collar? To say that not many kids are interested in computer science today…well, I’d say, add value to computer science, so it’s not just computer science, but computer science with a business, manufacturing or healthcare angle.
Technology is all around us. Even in the building of the Innovation Center, it is a whole different workspace than before. Or the idea of microgastronomy—where you get your food. It makes sense to get food locally; it doesn’t make sense to ship a bottle of water from France. While our fuel prices are temporarily low, they will likely spike in the future, and until we improve that transportation chain, it makes no sense. That supports the micro-economy here. The same thing with electronics. We want to grow our knowledge base and have smarter workforce development. Talk to John Erwin at ICC—he’ll tell you there isn’t a recession at ICC, they’re boomtown right now. How great is that? iBi