Parsec Moves Mountains in Time and Technology
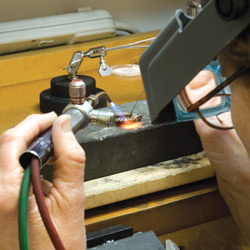
When it comes to expert service and technology, timing is everything. And nobody knows this better than the watchmakers and technicians at Parsec Enterprises.
When Marc and Diedre Young began Parsec Enterprises in 1977, they could not have imagined the success 33 years would bring. Embarking on a quest for opportunity with limited knowledge and a will for change, the couple founded what is today respected as one of the largest watch facilities in the nation.
Marc spent his early years working in the Indiana Department of Public Welfare. In the mid-1970s, he worked in consulting after graduating from Indiana University in 1973. But bureaucracy, Marc claims, was not his forte. “[My wife and I] were really looking to do something different,” he says.
Over time, Marc became intrigued by the quartz watch, which was all the rage in the mid-1970s. “It was a little bit like the iPod in that industry,” he says.
The quartz watch brought major shifts in horology—the science of timekeeping.
And no wonder. With the ability to measure time by means of a paper-thin piece of synthetic quartz, the unique timepiece possessed the technology to perform much more accurately than the mechanical watch. Quartz, claims Marc, “revolutionized watch making completely.”
With watch repairers accustomed to manipulating the gears and moving parts of mechanical watches, technicians attempting to fix quartz digital watches found themselves in a quandary.
“It was a paradigm shift in the entire industry,” Marc says. “The people who were doing repairs, they looked at a digital watch and didn’t know what they were seeing. There were no gears, there were no springs, there was nothing mechanical at all…It was a tremendous shift, a tremendous change, and for some reason, this came to my attention.”
Marc began asking numerous jewelers and retailers how they would repair a digital watch. “Throw it in the trash” became a popular answer. “I think it was just a matter of seeing that nobody was fixing these things and nobody really wanted to,” he says.
Although they lacked sufficient training in the industry, Marc and his wife set out to “build Rome” and establish their own watch repair company.
Small Beginnings
Marc and Diedre’s pursuit began as a part-time job. About two months into their work, Marc decided to “go all out with it.” The first week, they had just eight watches to repair. “It was tough for about five years,” he said. “The industry was changing.”
Still, he and his wife worked around the clock—no pun intended—to keep the business alive. After Zales Jewelers closed its service center, Stanley Zale gave Marc a corporate list of all the company’s stores. Watches were shipped to Marc from across the country. Demand skyrocketed from eight to 80 watches a week.
After setting up an exclusive situation with Gordon’s for a time, Marc and Diedre eventually moved from Indianapolis to Peoria in 1983, where they worked from the basement of their home. Today, Parsec has serviced more than 1.4 million watches of nearly every major brand and has 35 employees with a total of over 150 years of bench experience.
Building Trust
Although Parsec provides on-the-job training, Marc claims the ideal employee possesses an interest in problem solving and electronics and will work well with small tools and equipment.
“(The people we hire) have to like it,” says Marc. “They have to get gratification from seeing something that’s not working, working.”
And for Parsec employees, there’s never a dull moment. Workers have plenty of responsibilities, including cutting crystals, buffing and polishing, and performing water-resistant testing, to name a few.
“You have to have people you can trust…in their abilities and in their interest level to actually take the business and make it their own,” says Marc.
A Distinguished Name
Although Parsec’s employees keep the company ticking, part of Parsec’s value rests on the limited number of watchmakers in the nation. According to Marc, there are approximately just six thousand watchmakers in the United States—about half of which are retired.
Watch making schools spend 80 to 85 percent of their time teaching students about mechanical watches, even though mechanical timepieces make up only one percent of watches sold in the U.S. “What does that tell you about the other 99 percent?” asks Marc. “Is there a need for people to [fix non-mechanical watches]? Yes, there is. And that’s what we do.”
Parsec is also praised for its large capacity for volume work. “One year, we did 360,000 battery changes for a single company,” says Marc.
Other services include clock repair and in-house custom dial imprinting. Parsec prints logos on dials for companies and institutions and also engraves logos on the back of watches using computerized engraving.
One of Parsec’s most exclusive products is the Coinwatch. A relatively new product, Marc claims watch technicians will cut a coin—such as a dime—in half, drill holes in the center, and use the coin as the watch face. Parsec serves as a distributor for Coinwatch in North America.
The Right Technology
Parsec offers custom crystal cutting services using Kronoglass cutters that help technicians fashion out-of-production crystals to watch cases. Employees also use a LaserStar welder that helps technicians repair “difficult” jewelry, such as watches with titanium bands.
“Some watches have tiny bands with woven threads of gold,” says Marc. “If that tears, you can’t use a torch to weld it back together. But with the LaserStar welder, you can…do a very precise weld basically under a microscope without burning your fingers or melting all those threads into a blob.”
Parsec’s conventional jewelry soldering allows technicians to use a small torch with a tiny flame to repair intricate details, such as pendants and prongs on rings.
“Only because Diedre has become an accomplished database developer in her own right, and designed Parsec’s internal data network, can Parsec efficiently handle such high-volume projects and weekly customer repair numbers averaging 1,000 watches per week from retailers and consumers nationwide,” says Marc.
An important part of that system is Parsec’s intricate defect coding process, which gives manufacturers important, precise and specific knowledge of any product defects. “It incorporates what we know to be common failure points for watches, and we can put that into a data profile so manufacturers can use it to improve the product,” says Marc.
Better Than Before
Looking ahead, Marc says he would like Parsec to become more involved in the manufacturing aspect of watches. His primary goal is to remain at the forefront of the watch service industry.
“We’re going to continue with a more diversified customer base,” Marc says, “and grow the business intelligently and smoothly by improving our service offers. It’s an ever-changing challenge.”
To learn more about Parsec Enterprises, log onto parsecent.com, call (309) 689-6531, or visit their offices at 7501 N. Harker Drive, just off of Pioneer Parkway in Peoria. iBi